Damage to the turbo blades and balance issues caused by small objects entering the turbine or intake snail at high speeds.
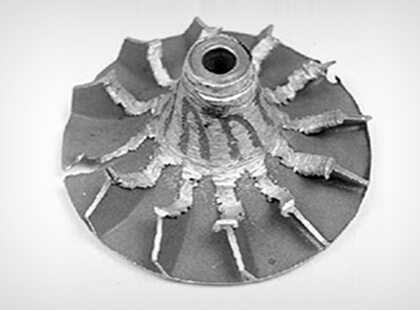
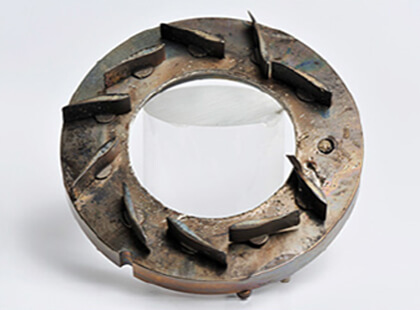
Drawing on our extensive work experience and strict quality policy, we offer only high-quality services for the repair and renewal of turbochargers.
The professional repair of turbochargers is carried out by skilled, specially trained personnel using the most modern and reliable equipment.
Our experts will provide advice on the repair and operation of turbochargers, assist in determining the causes of turbocharger failures, make a full diagnosis, and evaluate all the features of the turbocharger and its components.
Thanks to first-class modern equipment, our experts will be able to restore your turbocharger and handle tasks of eliminating turbo failures of any complexity.
For all works related to the repair of turbochargers, our company provides a long-term warranty in accordance with our quality policy.
We service and repair Automotive, Heavy Machinery, Marine, and Bus/Truck turbos using original spare parts and repair kits, all with a guaranteed warranty.
In a wide variety of industries and applications, numerous different turbochargers are used in both diesel and gasoline engines. Although these turbochargers may vary slightly in size, shape, and configuration, they all operate in the same way and contain the same basic components.
In this article, you will gain more information about the different parts and components that make up a turbocharger and understand what they do.
The compressor housing is where clean air is collected and compressed before being forced into the engine. It houses the compressor wheel.
_In modern turbochargers, this is typically made of aluminum and often has a 'spiral' or helical design that aids in providing optimal airflow and pressure to the engine.
The compressor wheel sits inside the compressor housing and is typically made of lightweight aluminum. During operation, this wheel spins at high speeds, drawing in air to be compressed and forced through the helical compressor housing into the engine.
This circular piston ring provides a flexible seal between the pressure ring and the back plate of the turbocharger. It is a small but vital part of the turbocharger, ensuring oil control and preventing contaminants from entering the bearing system from the compressor.
Also known as the seal plate, this plate connects the bearing housing to the compressor housing and acts as a retaining device for the thrust bearing system. The back plate serves as a closed barrier to prevent pressurized air from entering the bearing housing.
As the name suggests, the bearing housing contains the thrust bearing and journal bearings, providing lubrication circuits for their free operation. In some turbochargers, the bearing housing also incorporates a water-cooling system. Bearing housings are typically made of heavy cast iron.
Located inside the bearing housing, the thrust bearing controls the axial movement (in and out movement) of the turbine shaft between the compressor wheel and the turbine wheel. As the turbine and compressor wheels spin at high speeds, the thrust bearings must be well-lubricated with oil to prevent friction and wear.
Also found inside the bearing housing, the journal bearings control the radial load. Practically, this means supporting the rotating parts of the turbo (turbine wheel, shaft, and compressor wheel) and allowing them to spin freely without swaying too much up and down. Journal bearings are held in place with bearing clips.
Located behind the bearing housing, between the housing and the back face of the turbine wheel, the heat shield protects the turbocharger parts from the heat of the exhaust gases passing through the exhaust housing.
Typically made of cast iron or a high-temperature alloy, the turbine housing is used to collect exhaust gases from the engine and funnel them towards the turbine wheel. Like the compressor housing, it has a “curved,” helical design to maximize the speed of the passing exhaust gases.
The turbine wheel helps convert the energy from the engine's exhaust gases into kinetic energy, which is then used to drive the compressor wheel.
Turbine wheels generate a lot of heat during operation and are typically made from durable, lightweight, and heat-resistant alloys.
This circular ring provides a seal between the bearing housing and the turbine wheel. It has two purposes: to prevent oil from entering the turbine housing and exhaust gases from entering the bearing housing.
The shaft nut holds the compressor wheel and the pressure ring onto the turbine shaft, ensuring they all rotate as one.
Also known as the wastegate actuator, this is a valve that directs exhaust gases away from the turbine wheel. It helps control the speed of the turbine, preventing it from over-speeding, and consequently regulates the speed of the compressor, and thus the boost pressure. This helps shut off the turbo at its maximum safe pressure, protecting the turbocharger from unnecessary wear.
When the turbine wheel, thrust bearing assembly, compressor wheel, and shaft nut are all connected, it is known as the rotary assembly. It is important to remember that these parts are designed to work together, and changing one element of the assembly can have a knock-on effect on the other components.
Also known as relief valves, bypass valves are designed to prevent turbo compressor surge. They help reduce wear on both the turbocharger and the engine itself during gear changes. This is done by allowing pressurized air to escape from the turbo to the atmosphere or redirecting this air back to the air intake when the engine's revs change.
When looking at Turbo Fault Diagnosis from a broad perspective, different symptoms emerge. General symptoms that indicate a turbo failure include;
Damage to the turbo blades and balance issues caused by small objects entering the turbine or intake snail at high speeds.
Friction and high temperatures resulting from oil entry restrictions, improper placement of gaskets, and the use of liquid gasket or low-quality lubricants, leading to cracks and material transfer due to turbo overworking.
Damage to the turbo bearing system caused by suspended high-density carbon in the oil due to long oil change intervals or insufficient maintenance. Bearing damage caused by suspended steel casting balls in the oil after major engine maintenance.
Damage due to operating the turbo beyond its design values or outside the specifications stated by the vehicle manufacturer. Maintenance issues, engine malfunctions, or performance enhancements made by non-experts and unauthorized persons can pull the turbo rotation speed beyond operational limits, causing failure due to overworking of the compressor and turbine blades.
Atatürk Oto Sanayi Sitesi 1. Kısım 45. Sokak No: 42, 34485 Sarıyer
+90 545 404 34 44
maslakturbo@gmail.com
Monday - Saturday 09:00-19:00